✔ The solar cells in traditional solar panels are made of crystalline silicon
✔ Solar cells are stuck onto a clear pane and connected with metal wires
✔ A backsheet and frame are sealed onto the clear pane to form an airtight unit
Making a solar panel is a somewhat complicated process, which involves several steps. This explains why solar panels cost a decent amount of money.
We’ll break down how solar panels are manufactured and explain the different steps in this article. We’ll also go over how non-traditional types of solar panels are made, and tell you where most solar panels are manufactured.
But if you’re curious how solar panels actually work, we’ve got you covered, too. Use our guide to find out not only how they work, but how they generate electricity, too.
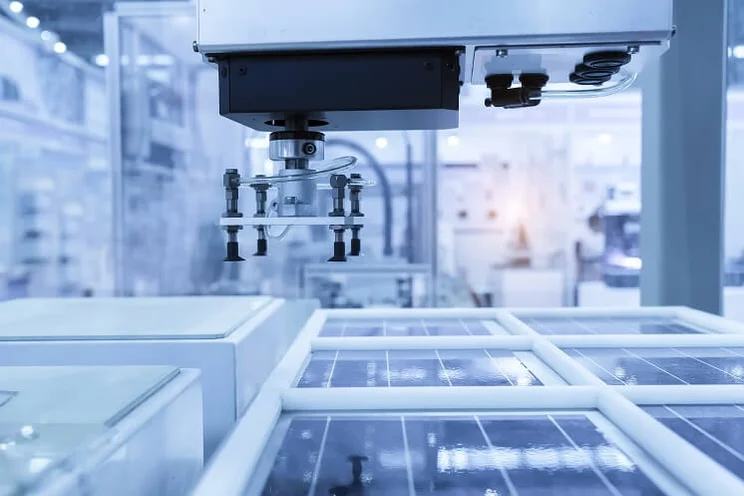
How are solar panels manufactured?
Solar panel manufacturing involves making solar cells from crystalline silicon (a very pure form of silicon), assembling them onto a clear pane, connecting the cells with wiring, fitting a backsheet over them, and encasing everything in a frame.
Solar cells are the most important part of the solar panel, since they’re the part that generates electricity.
The main two types of solar panel used in residential settings are monocrystalline and polycrystalline solar panels.
We’ll take a more in depth look at how these two types of panels are made in the sections below.
1. The crystalline silicon is melted into cylinders
To make monocrystalline solar cells, a single fragment of crystalline silicon is melted down and moulded into a cylindrical shape, often called an ingot. During this process, the crystalline silicon is also mixed with gallium or boron, which gives it a positive electrical charge.
To make polycrystalline solar cells, the process is more or less the same. The only difference is that several crystalline silicon fragments are melted together, instead of one.
Crystalline silicon is a photovoltaic (PV) material, which means it can convert sunlight into electricity. Other types of solar panels use different PV materials.
2. The silicon cylinder is cut into wafers to form solar cells
The silicon cylinder is then cut into paper-thin wafers. A layer of phosphorus is added to one side of the wafers so that it has a negative electrical charge. The other side (the boron or gallium side) will keep its positive charge – this is to control the flow of electrons, and is similar to how a battery functions.
As a last step in this process, an anti-reflective coating is added to the wafers, so that they absorb sunlight instead of reflecting it. At this stage, the wafers are now fully formed solar cells.
3. Metal electricity conductors are printed and wired into the solar cells
Thin strips of metal, typically silver, are printed onto the front of the solar cells. Next, the solar cells are connected together from the back by thin wires, usually made from copper.
These metal strips and wires are electricity conductors. In simple terms, this means that they gather and move the electricity that’s generated when the solar cells are exposed to sunlight.
4. The solar cells are attached to a clear pane
The solar cells are then stuck face down onto a pane of glass or clear plastic coated with a sheet of adhesive material, such as polymer encapsulant or ethylene-vinyl acetate (EVA). The solar cells end up forming a grid pattern on the pane.
The clear pane serves as a protective front layer, which keeps the solar cells safe from rain, dust, or debris.
5. The clear pane is attached to a backsheet
Another layer of adhesive materials is added over the face-down solar cells, and a backsheet (the protective backing of a solar panel) is added over that, essentially sandwiching the solar cells in between protective layers.
All the layers are then heated and vacuum pressed together, so that they bond into a tight unit. At this stage, the solar panel is almost finished.
6. A frame and a junction box are attached to the solar panel
Metal circuit ribbons are attached to the edges of the solar panel, followed by a metal frame, typically made from aluminium. The frame makes the panel sturdier and more resistant.
The circuits that run along the edge of the solar panel are connected to a junction box, which is attached to the back of the panel.
The junction box collects the electricity generated by the panel’s solar cells, and regulates the amount of electricity being sent from the panels to the rest of the electrical system they’ll be connected to.
With this final step, the solar panel is complete.
7. Testing happens throughout the manufacturing process
The solar panels and solar cells are tested for faults at all stages of the manufacturing process. Engineers regularly check for cracks in the solar cells or panels, and expose them to light to ensure they work.
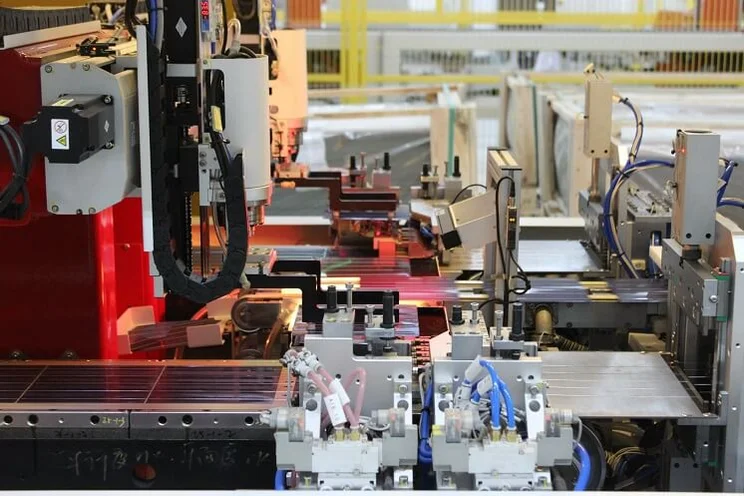
How are other types of solar panel made?
There are other types of solar panels, beside monocrystalline and polycrystalline. These include thin-film solar panels, organic solar panels, perovskite solar panels, quantum dot solar panels, and ‘zombie’ solar panels.
The process of sandwiching solar cells between protective layers remains the same, but what the solar cells are made of and how they’re made changes depending on the type of panel.
We’ll get into how different types of solar panel cells are made in the following sections.
How are thin-film solar panels made?
To make thin-film solar panels, the PV material is laid out in several thin layers onto a flexible glass, plastic or metal sheet, instead of being pre-cut into cells, as is the case with monocrystalline or polycrystalline solar panels.
Several different types of PV material are used to make thin-film solar panels. These include cadmium telluride (CdTe) – the most common material for thin-film panels – copper indium gallium selenide (CIGS), and amorphous silicon (a-Si).
Once the PV material has been laid out, a laser carves rectangular patterns into it to create individual solar cells.
How are organic solar panels made?
Organic solar panels have solar cells made from ‘organic compounds’. These are molecules composed of carbon atoms bonded by other atoms, such as hydrogen, oxygen, and nitrogen.
The result is a very lightweight and flexible solar cell, which can be placed on a wide variety of supportive materials, from glass to flexible plastic. The downside is that organic solar cells are less efficient than typical solar cells – only around 10% efficient on average – and they degrade much faster too.
Because of this, and the fact that the technology is still fairly new, organic solar panels aren’t yet commercially available.
How are perovskite solar panels made?
Perovskite is the PV material used in perovskite solar panels. It’s a synthetic material that imitates the structure of a mineral with the same name.
It’s a relatively new form of technology, and so researchers are still looking for the best way to manufacture perovskite solar panels.
For now, there are two main methods for making perovskite solar cells.
The first method is to coat a standard silicon solar cell with a thin layer of perovskite. This is usually done using a “spin-coating method”; a few drops of a perovskite solution are poured onto a base (typically a solar cell) which is then spun until there’s an even layer of perovskite.
The second, more recent method, is similar to the method used for making thin-film solar panels. Basically, it means coating a sheet – made from plastic, glass, or silicon cells – with thin layers of perovskite.
How are quantum dot solar panels made?
In a quantum dot solar panel, ‘quantum dots’, which are basically artificial atoms, are the PV material.
The most common method for manufacturing quantum dots is called ‘colloidal synthesis’.
This process involves a lot of complex chemistry, but the final result is that the quantum dots are dispersed into a liquid solution, and sprayed or dropped onto a supportive material, such as a glass or plastic pane (the same kind used in other types of solar panels).
Quantum dot solar panels aren’t yet in use, since they utilise a relatively new technology to create solar cells. But studies have shown that they can produce solar panels that are potentially 66% efficient.
How are zombie solar panels made?
Zombie solar panels have ‘zombie’ solar cells, also called dye-sensitised solar cells. These cells are made from organic dyes that can absorb light.
To make them, a conductive mixture, typically titanium dioxide, is layered into a thin square of glass or plastic coated with a conductive material, usually idiom tin oxide or fluorine-doped tin oxide. This is then soaked in the organic dye.
After that, the square is dipped in an electrolyte solution and covered with another layer of glass, this time coated with a different material, typically platinum, carbon, or graphite.
Zombie solar panels aren’t commercially available yet, but what’s special about them is that they have the potential to generate electricity indoors, albeit in small amounts.
Where are most solar panels made?
Most solar panels are made in China – around 80% in fact, according to the International Energy Agency (IEA).
On top of that, six of the seven largest solar panel manufacturers are China-based companies, among them JA Solar and Aiko Solar, who make some of the most efficient solar panels.
This doesn’t mean that solar panels aren’t made in other countries. The USA and Canada also have large solar panel manufacturing companies, such as First Solar and Canadian Solar respectively.
Summary
Making a solar panel is a complex process that’s changing and improving all the time.
Monocrystalline and polycrystalline solar panels, which have silicon-based solar cells, might be the norm today, but maybe not in the future. New and more efficient types of solar panels, such as perovskite and quantum dot solar panels could become the norm in a few years.
That’s all good news for you, the consumer, since the more efficient solar panels are, the more electricity they’ll generate. Plus, with the cost of solar panels going down, that means you’ll break even on your purchase in less time than you would have ten years ago.